Keeping Cool Under Fire
This manufacturer in Hereford asked us to take a look at their cooling system which was starting to cause them issues. Their cross head forge was being cooled by a conventional ducted unit and condensing unit were mounted on a common mobile chassis.
The system in place was essentially made up of comfort cooling equipment which did not meet the 24/7 cooling demands of the forge. This made the system prone to breakdowns and required a higher frequency of service visits. Another issue with the current system was its close proximity to the forge which presented a serious health and safety risk for maintenance personnel. As a consequence this led to increased levels of production down-time in order to maintain the equipment having a negative impact on the productivity of the client’s business.
The Challenge
The client had the following requirements for the new system:
- A more resilient and robust alternative to the comfort cooling equipment.
- A solution which won’t cause production downtime because of access for servicing.
- A system which can also be mounted internally in the factory areas and therefore able to cope with being subjected to high temperatures.
- Differential temperatures across production equipment.
A bespoke cooling system
A new bespoke cooling system was designed by our in house design team to address the issues and requirements the client had. The new system has the following features:
Close control A/C
Cooling provided by a close control A/C unit which is designed to be located remotely from the cross head forge allowing easier access for maintenance and avoiding production downtime.
Twin condensers
Twin condensers were specified for this project because of their ability to be installed within the factory and cope with high temperatures.
Airflow delivery
A fully insulated rigid ductwork distribution system would be installed to ensure maximum airflow delivery to the cross head forge.
Differential temperature across production
A second ducted airflow distribution system would also be installed to discharge the hot air from the condensers to beneath the forge. This would result in providing a desirable differential temperature across the production equipment as required by the client to improve performance.
The Result
We installed the new system with the following results:
Fewer attendances
The new installation allowed the old system to be removed and has resulted in fewer attendances being required to service and maintain the equipment.
Reduced running costs
Given the higher sensible heat ratio of the new system (the amount of actual ‘useable’ cooling effect, compared with the total output of the equipment), we also estimate that the new system has reduced running costs by approximately 33%.
Cross Head Forge Cooling Plans
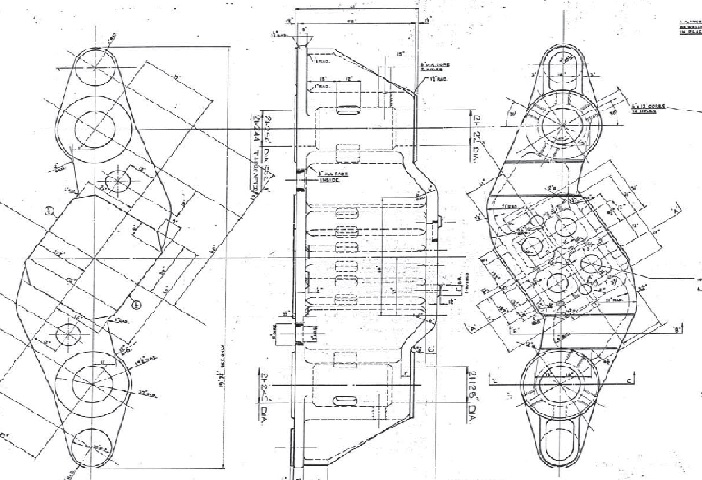
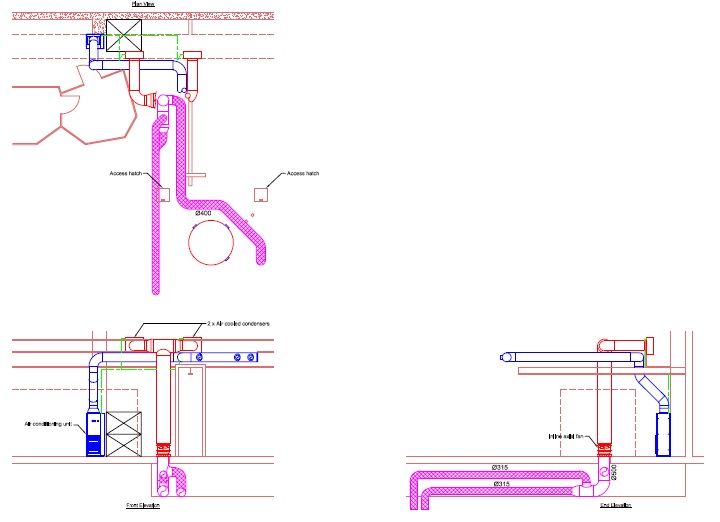